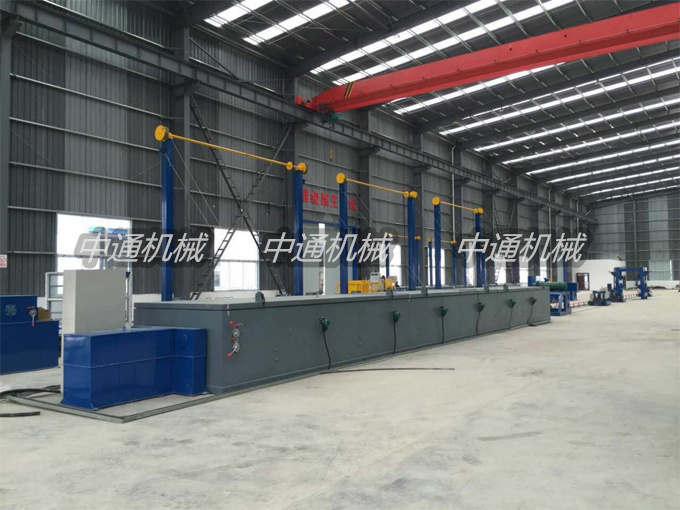
在现代工业生产中,多面固化炉扮演着重要的角色,尤其在复合材料行业、电子制造业以及涂覆工艺等领域。正确设置和调整固化参数不仅关系到产品的质量,还直接影响到生产效率。本文将探讨如何调整多面固化炉的加热和冷却参数,旨在实现固化效果和提高生产效率。
首先,了解材料的固化特性至关重要。每种材料,无论是环氧树脂、聚氨酯还是其他合成物,都有其特定的固化温度和时间。这些参数通常由材料供应商提供,并应在实验环境中进行验证。理解材料的流变学特性、热特性以及反应动力学是设定固化参数的基础。
接下来,考虑产品的形状和尺寸。不同形状和大小的制品对热量的吸收和散发能力不同,这直接影响到加热时间的设定。较厚或较大的制品需要更长的时间来使中心区域达到所需温度。因此,加热参数必须根据具体产品的特性进行调整。
在设定加热参数时,应采用逐渐升温的方式,避免温度冲击导致材料产生应力或裂纹。一个常见的做法是分为预热、加热和保温三个阶段。预热阶段将温度缓慢提升至接近固化温度;加热阶段快速达到固化温度;保温阶段则维持恒定温度以确保材料彻底固化。
冷却过程同样重要。太快的冷却速率可能会导致材料因热应力而变形或开裂。理想的冷却过程应该是可控并且均匀的,以避免温差引起的内部应力。冷却参数的设定应考虑到材料的玻璃转化温度(Tg)以下,确保材料在出炉前已足够硬化,从而防止变形。
在实践中,加热和冷却参数的优化是一个迭代的过程。生产人员应记录每次固化过程的数据,包括温度曲线、产品品质检验结果等,以便分析并调整参数。通过持续的监控和调整,可以逐步找到固化条件。
此外,使用先进的控制系统和软件可以实现更加的参数控制。例如,采用可编程逻辑控制器(PLC)和集散控制系统(DCS)能够实时监控固化炉内的温度分布,并根据反馈自动调节加热器功率和冷却速率。这不仅提高了控制的精度,也减少了人为错误的可能性。
为了进一步提高效率,可以考虑引入能量回收系统。在冷却阶段,大量的热能被排放到环境中。通过能量回收系统,这部分热能可以被重新利用于预热或其他工艺流程中,既节约了能源又减少了生产成本。
定期维护和清洁固化炉也是保证操作条件的关键。积垢和灰尘会影响热交换效率,导致不均匀加热。保持设备的良好状态确保了一致且可靠的性能。
综上所述,调整多面固化炉的加热和冷却参数以达到固化效果并提高生产效率是一个综合性的任务。它涉及对材料特性的深入理解、对产品要求的细致考量、对设备性能的控制以及对整个工艺过程的不断优化。通过以上措施的实施,可以实现产品质量的提升和生产效率的增加,达到降低生产成本和提高市场竞争力的目的。